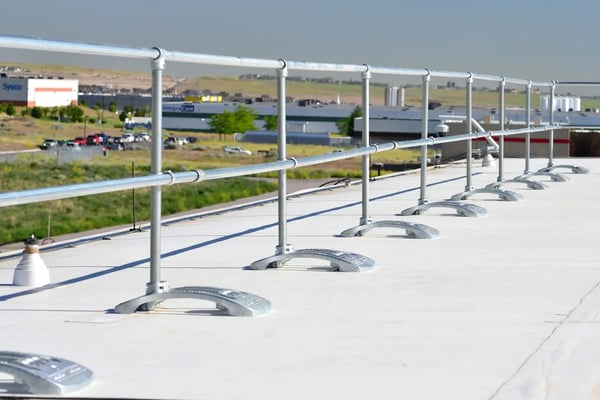
Understanding OSHA Requirements for Guardrail
As the leading resource on fall protection, we at Diversified Fall Protection are frequently asked for help understanding and complying with OSHA requirements for guardrail and safety railing systems.
Below, we’ll explain OSHA’s official rules on guardrail for general industry applications and show you how your business can remain compliant with these regulations.
For more help, contact the team of experts at Diversified Fall Protection. Our engineers will design and implement a complete, OSHA-compliant guardrail system to protect your team when working on rooftops and other elevated surfaces.
When is guardrail required?
OSHA requires guardrails on any walking-working surface that is 4 feet or more above a lower level. Additionally, stairways with 4 or more steps must have a stair rail system with a handrail. If employees are working near dangerous equipment, guardrails are required at any height to prevent falls.
What is a guardrail?
A guardrail, or guard rail, is a stationary, fixed fall protection system designed to prevent workers from stepping over the edge of a walking-working surface. OSHA 1910.29(b) is the portion of the regulations that contains system requirements that employers must follow to ensure guardrail systems will protect workers from falling to lower levels.
Three main parts of a guardrail
There are three main parts of a guardrail: The top rails, the midrails, and the vertical posts. Each part of the guardrail must comply with OSHA’s rules, including material type, size, height, and location. We explain each of these below.
Guard Rail Dimension Requirements
Above the OSHA Figure D-11 diagrams illustrating guardrail heights and gap requirements:
-
42-inch (+/- 3 inches) top rail or 107cm (+/- 8 cm)
-
Midrail halfway between top rail and working surface
-
Vertical balusters spaced no more than 19 inches (48 cm) apart
Diversified Fall Protection provides turnkey guardrail systems that comply with all of the following OSHA requirements for guard rail.
Railing height for guard rail
According to OSHA, top rails (or equivalent guardrail system members) must be 42 inches (107 cm), plus or minus 3 inches (8 cm), above the walking-working surface. The top edge height may exceed 45 inches (114 cm), as long as the guardrail system meets all other criteria.
Guardrail is required for any platform 4 feet or higher above a lower floor or the ground. Guardrails are required have vertical heights of 42 inches from the upper surface of the top rail to floor, platform, runway, or ramp level.
Mid-rails
If there is not a wall or parapet at least 21 inches (53 cm) high, then midrails must be installed halfway between the top edge of the guardrail and the walking-working surface. Screens, mesh, intermediate vertical members, solid panels, or other equivalents can be considered “midrails” for this purpose.
If screens and mesh are used, they must extend from the walking-working surface to the top rail and along the entire opening between top rail supports.
Intermediate vertical members (such as balusters) must be installed no more than 19 inches (48 cm) apart. Other equivalent intermediate members (such as additional midrails and architectural panels) should be installed so that the openings are not more than 19 inches (48 cm) wide.
Guard rail strength
OSHA requires guardrail be strong enough to withstand force both outward and downward along the top rail and at the midrail section.
Guardrail systems need to be capable of withstanding a force of at least 200 pounds (890 N) at any point along the top rail. This force is applied in a downward or outward direction within 2 inches (5 cm) of the top edge. When tested in a downward direction, the top rail of the guardrail system must remain at least 39 inches (99 cm) above the walking-working surface.
Midrails, screens, mesh, solid panels, and other equivalent intermediate members must be capable of withstanding, without failure, a force of at least 150 pounds (667 N) applied in any downward or outward direction at any point along the intermediate member.
Smooth surfaces required for guardrail
Guardrail systems need to be smooth-surfaced. This is to protect employees from injury, such as punctures or lacerations, and to prevent catching or snagging of clothing. Our railings have a powder-coated finish to meet this requirement.
OSHA also requires that the ends of top rails and midrails do not overhang the terminal posts, which are the posts at each end. The only exception is if the overhang does not pose a projection hazard.
Similarly, steel and plastic banding are not permitted to be used for top rails or midrails, and guard rails must be at least 0.25-inches (0.6 cm) in diameter or in thickness. These requirements also protect workers from injury caused by too much force applied at these points.
Guardrail near hoist areas and holes
OSHA says that when guardrail systems are used at hoist areas, there needs to be a removable guardrail section placed across the access opening when employees are not performing hoisting operations. This section must have a top rail and midrail. You may use chains or gates instead of a removable guardrail section if you show they provide the same level of protection as guard rails.
Guardrail systems used around holes must be installed on all unprotected sides or edges of the hole. If materials will be passed through the hole, no more than two sides of the guardrail system can be removed at a time. When materials are not being passed through the hole, the hole must be guarded by a guardrail system along all unprotected sides or edges or closed over with a cover.
Guardrails at point-of-access holes
When used around holes that serve as points of access (such as ladderways), the guardrail system opening needs to have a self-closing gate that slides or swings away from the hole. The gate must have a top rail and midrail (or equivalent intermediate member) that meets the requirements for guardrail above. The other option is to offset it to prevent an employee from walking or falling into the hole.
Guardrail for ramps and runways
For ramps and runways, guard rail must be installed along each unprotected side or edge. You can use Manila or synthetic rope for top rails or midrails if it is inspected as necessary to ensure that the rope continues to meet OSHA strength requirements described above (the 200-pound and 150-pound tests).
Where to Find OSHA-Compliant Guardrail?
As you can see, there are a lot of OSHA regulations to follow when choosing guardrail for your business. Failure to do so will put your employees at risk, not to mention open you up for possible litigation in the event of an accident, as well as fines for noncompliance.
Diversified Fall Protection provides a range of OSHA-compliant guard rail and safety railing to protect your team. We make it easy for your business to install OSHA-compliant guardrail systems, with our engineered turnkey approach. To request a quote and get started, contact us.
Schedule an assessment with Diversified Fall Protection
Contact Us to request a fall safety review