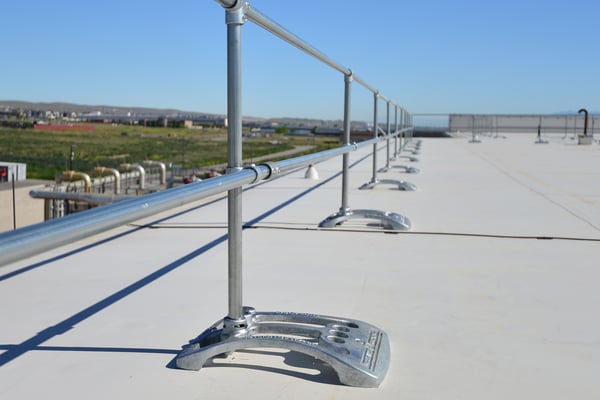
Understanding the Differences: Federal OSHA vs. Cal/OSHA Fall Protection
Navigating the complex world of workplace safety can be challenging, particularly when understanding the differences between federal and state regulations. However, companies can better protect their employees and minimize work-related injuries and illnesses by understanding these crucial differences. This article delves into the critical distinctions in fall protection between federal OSHA and Cal/OSHA that businesses operating in California need to be aware of.
State approved OSHA programs
Federal OSHA operates under the United States Department of Labor, striving to ensure the safety and health of American workers through various initiatives such as training, education, and outreach programs. The agency also oversees and approves state and territorial workplace health and safety programs.
Typically, state health and safety plans align with federal OSHA guidelines, with each state plan required to address all aspects of the federal OSHA plan at a minimum for approval. OSHA supervises these plans to ensure they are at least as effective as the federal OSHA in protecting workers and preventing work-related injuries, illnesses, and fatalities.
Federal OSHA approved California's state health and safety plan in 1973. Cal/OSHA enforces this plan, which caters to California's unique needs through the development of specific standards and practices. So, let's look at a few of the most significant differences between Federal OSHA and Cal/OSHA as it relates to fall protection.
Fall protection trigger height
Federal OSHA mandates fall protection for employees working 4 feet above a lower level in general industry and 6 feet in construction. In comparison, Cal/OSHA requires fall protection for employees working 30 inches above the level below in general industry and sets specific fall protection trigger heights for construction based on the task performed.
These trigger heights include 2 stories or 30 feet for connecting structural steel, 20 feet for most roofing work, and 15 feet for panelized roof systems, residential framing and roofing activities, and work on wider structural members. In addition, it requires fall protection at a height of 7 ½ feet for unprotected platforms, scaffolds, or edges of structures and 6 feet for working with rebar or similar projections.
Guardrails
Cal/OSHA favors guardrail systems more than Federal OSHA
While there are similarities between the federal OSHA and Cal/OSHA minimum requirements for guardrail systems, there are also some differences.
Top Rail
As per federal OSHA 1910.29(b)(1), the top rails or similar members of guardrail systems should be positioned at a height of 42 inches (107 cm), give or take 3 inches (8 cm), above the surface used for walking or working.
In contrast, Cal/OSHA Title 8, 3209(a) mandates that the vertical height of the top rail should fall between 42 inches and 45 inches from the upper surface of the top rail to the level of the floor, platform, runway, or ramp. In addition, the height dimensions must not deviate by more than one inch.
Load capacity
Federal OSHA and Cal/OSHA have established regulations that mandate guardrail systems to withstand a minimum force of 200 pounds applied in a downward or outward direction at any point along the top rail within 2 inches of the top edge (1910.29(b)(3)).
In addition, Cal/OSHA Title 8, 3209(b) specifies that all types of permissible guardrails, including their connections and anchorage, should be designed to bear a live load of 20 pounds per linear foot that is either applied horizontally or vertically downward at the top rail.
Fall protection inspections
As equipment becomes worn and damaged over time, it eventually reaches a point where it is no longer as effective and may pose an even greater risk to the user. To ensure the safety of workers, California mandates that all fall arrest systems and their components be inspected and documented twice a year by a competent person in fall protection. At the federal level, these inspections occur annually, with some equipment requiring more frequent assessments to ensure they remain in good condition.
The guidelines of an OSHA fall protection inspection require regular inspection of all fall protection equipment, including harnesses, lanyards, SRLs, and lifelines. During these inspections, a qualified individual, known as a competent person, will assess the equipment in line with manufacturer requirements for bi-annual and annual inspections.
We're here to help
Understanding the nuances between federal OSHA and Cal/OSHA fall protection regulations is vital for businesses operating in California. By staying informed, companies can establish a safer work environment, safeguard their employees, and reduce work-related injuries and illnesses. To do that, employers must commit to regular fall protection inspections and diligently maintain their safety equipment's integrity.
Diversified Fall Protection offers turnkey solutions for fall prevention systems and equipment, including fall protection inspections. As your fall safety partner, we provide on-call expertise to ensure your systems and equipment remain in optimal condition. Our comprehensive fall protection solutions encompass fall arrest system design, installation, training, and inspection. Let us help you create a safer and more compliant workplace.
Schedule an assessment with Diversified Fall Protection
Contact Us to request a fall safety review